Photogrammetry vs Lidar Remote Sensing
As remote sensing technology continues to develop and improve, we’re seeing more potential uses and opportunities to create value in new industries and fields of study, from environmental science to public safety to telecommunications.
Several different remote sensing methods are available today, and each one comes with strengths and limitations. Some will be well-suited for one application but not others. How do you determine which is best for your industry?
In this post, we’ll go over two popular remote sensing technologies, LiDAR and photogrammetry, and discuss some key differences between them.
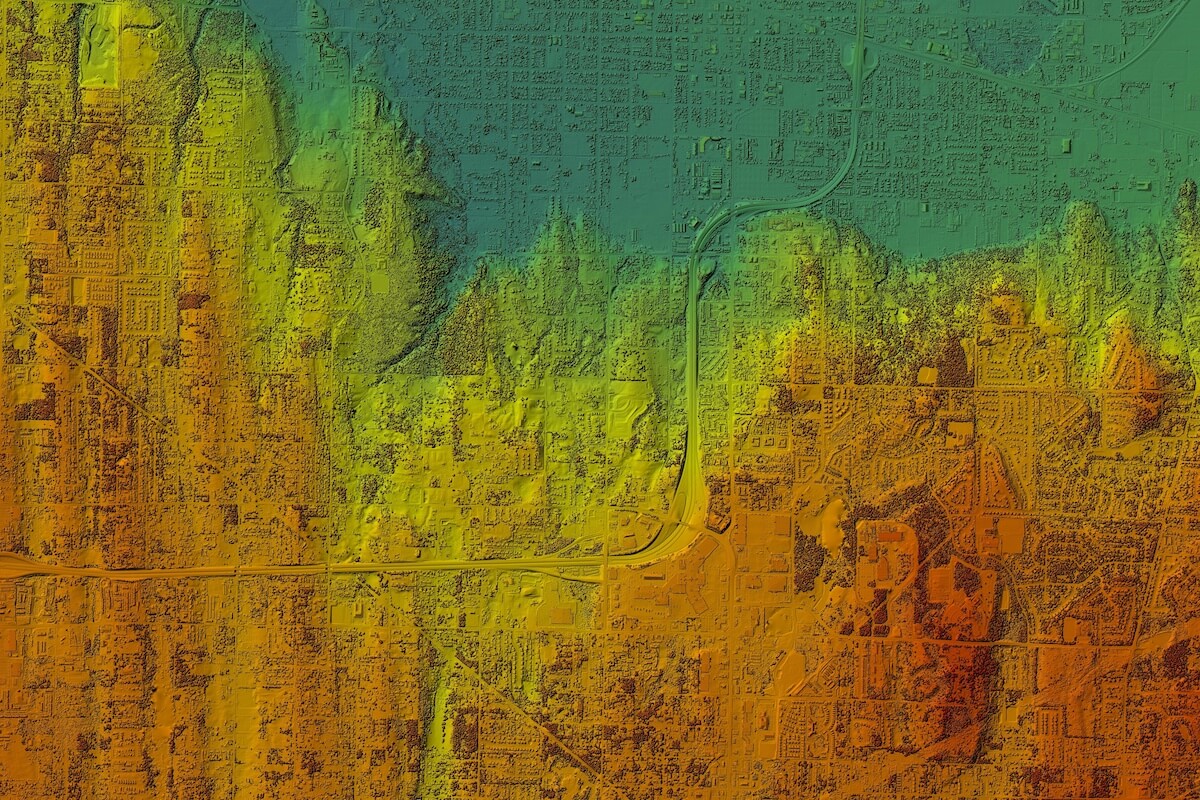
LiDAR vs. Photogrammetry: A Two-Minute Primer
Remote sensing allows people to capture and collect important environmental or structural data faster and more accurately than ever before. Here’s a breakdown of two popular data collection practices: LiDAR and photogrammetry.
What is LiDAR?
LiDAR, or light detection and ranging, uses points of light to create a detailed map of an object’s position in space. It has been used to power everything from automated driving technology to augmented reality to advanced topographic surveying.
When mounted from an unmanned aerial vehicle (UAV) or airplane, LiDAR can be used to directly measure the height and density of land and vegetation below, including detailed data on ground cover and trees. This remote sensing method is valuable for mapping structure, density, and other local characteristics of large land parcels from overhead.

What Is Photogrammetry?
Photogrammetry uses image overlap and UAV-captured images to produce a robust 3D composite of a region. By using ultra high-resolution image collection in concert with advanced GPS and mapping software, photogrammetry can produce a fully immersive 3D visual model of the real world. More than a survey map, this process creates an interactive photographic artifact that can be deployed by environmental agencies, construction firms, utility companies, and more.
Popular Use Cases for LiDAR Remote Sensing and Photogrammetry
LiDAR | Photogrammetry | |
---|---|---|
Mining and geology | ✓ | ✗ |
Forestry management | ✓ | ✓ |
Hazard assessment | ✓ | ✓ |
Agriculture | ✓ | ✓ |
Construction | ✗ | ✓ |
Telecommunications | ✗ | ✓ |
Oil & Gas | ✗ | ✓ |
First response | ✗ | ✓ |
Surveying | ✓ | ✗ |
What else can remote sensing do? Here are some examples in the news from across various industries and disciplines:
- Remote sensing applied to estimate lake clarity in China
- Using remote sensing to get the full potential out of grain crops
- Studying penguins without disturbing their habitat
Want to learn more about remote sensing technology? Read our Complete Guide to Remote Sensing.
How does LiDAR work?
LiDAR uses basic physics and geometry to uncover remarkable insights. To do so, it uses the power of a laser directed down toward the earth’s surface and fired in rapid succession—in most cases, at a rate of many thousand pulses per second. The amount of time it takes for the light to return to the source indicates its exact distance. LiDAR works like echolocation in bats or submarines, but it’s powered by the incredible speed of light (about 186,000 miles per second, if you’re keeping score at home).
Data generated by LiDAR sensors is collected and pinned to GPS metadata to create a detailed map of the landscape. To produce an accurate picture, data from remote sensing tech is then layered to cross-reference ground points and flag errors and inaccuracies.
A LiDAR instrument typically uses three component pieces to collect data:
- A laser produces light that is used as the measurement medium.
- Reflected light from the ground is collected by the photodetector sensor and optics.
- A GPS receiver documents the exact position of thousands of data points in real time.
Popular Remote Sensing Use Cases for LiDAR
- Surveying
- Augmented reality
- Automated driving
- Hazard assessment on lava flows, landslides, tsunamis, and floods
Types of LiDAR
LiDAR can be deployed in a number of ways depending on the application and the type of data capture required, including:
- Terrestrial: Either static or mounted on a moving vehicle, this type of LiDAR is best suited when a detailed view of the ground is desired.
- Airborne: When the goal is to capture data across vast areas, LiDAR cameras can be mounted on a drone or aircraft.
- Satellite: For an even larger bird’s-eye view, satellite-mounted LiDAR captures data about the atmosphere in addition to the terrain below.
Challenges and Opportunities in LiDAR Remote Sensing
As with any type of technology, LiDAR remote sensing has advantages and disadvantages. The primary challenges are around cost and reliability, while opportunities lie in its accuracy, speed, and functionality.
When compared to cameras, LiDAR equipment is more costly, and the expenses related to capturing data must also be considered. With multiple moving parts, LiDAR equipment must sometimes be repaired, potentially impacting its reliability.
Because it uses lasers, LiDAR delivers extremely accurate results and is able to capture small details in a short period of time. This high-resolution data can be used to create 3D maps that are useful for a broad range of applications.
How does photogrammetry work?
The defining feature of photogrammetry is the use of ultra high-resolution aerial photography. By capturing multiple images over a landscape, a “stereo” version is produced that provides software with differing views of a single focal point (for an example of how this works, look at a nearby object and alternate closing one eye and then the other). This shifting perspective creates scale that is used to create a composite image with accurate, measurable definition.
These photographs can collect enormous amounts of data from huge swaths of land. Like LiDAR, photogrammetry can be used to survey structures or properties with incredible accuracy. In addition, this remote surveying method produces a photographic document of on-the-ground conditions that can be used to perform surveillance, track changes in an environment, or create 3D interactive maps of a property.
Popular Remote Sensing Use Cases for Photogrammetry
- Construction
- Mining
- Telecommunications
- Oil and gas
- First response
Types of Photogrammetry
Just as with LiDAR remote sensing, photogrammetry can be captured on the ground (either static or mobile), in the air (from a helicopter, plane, or drone), or from space (with a satellite). The most appropriate method will depend on the application.
For example, a construction site might benefit from static photogrammetry to identify potential hazards or monitor progress. On the other hand, that same construction project might also benefit from drone photogrammetry to verify existing conditions or compare built conditions to drawings.
Challenges and Opportunities in Photogrammetry
Photogrammetry is a powerful tool, but in some cases, it might have limitations. For example, if there is low contrast or a uniform texture, it may be difficult to discern details in the images. Atmospheric conditions might also affect image quality, although this is often less of a concern with terrestrial and drone photogrammetry.
On the plus side, photogrammetry is comparatively less expensive than LiDAR remote sensing and comes with the same speed. Imagery provides an accurate, real-world snapshot of the terrain, structures, and other conditions with a high level of resolution.
What Sets LiDAR and Photogrammetry Apart?
Both LiDAR and photogrammetry are highly accurate for surveying buildings, infrastructure, and raw land. LiDAR can collect more detailed depth information than photogrammetry, but photogrammetry includes detailed visual information on the environment which is indispensable for many researchers.
When it comes to dollars-and-cents decision-making, LiDAR tends to be more costly and more difficult to set up and calibrate, especially when mounted on surveying airplanes and helicopters. However, the cost of both photogrammetry and LiDAR are dropping thanks to the widespread adoption of UAV technology across industries.
Read about how UAV photogrammetry can go beyond surveying and mapping to cut costs, improve data quality, and transform entire industries.
Choosing the Right Data-Processing Solution
Selecting the right approach to mapping is the first step, but finding the right partner for the job is equally important. Mapware has the remote sensing technology and the expertise to create value for you and your customers.
Mapware’s photogrammetry software is the best tool for the job, whether you want to map a single building, a dozen oil derricks, a protected wetland, or an entire city. This software suite generates bigger, better 3D maps that are fully cloud accessible for use in the field.
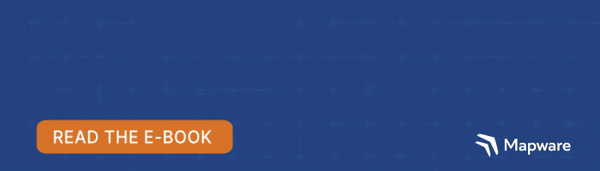
This article, originally posted on June 1, 2020, was updated April 27, 2023.